HydroFORM™ Scanner: The complete solution for comprehensive corrosion mapping
Published by Kristian Ilasko,
Digital Content Assistant
Hydrocarbon Engineering,
Inspectors need a reliable technique in order to inspect pipelines quickly and efficiently. The combination of the next-generation HydroFORM™ corrosion scanner combined with the OmniScan™ X3 flaw detector provides the complete solution for corrosion mapping. This pairing facilitates precise measurement of material thickness, simultaneous mapping of internal and external corrosion, and the detection of midwall damage, significantly streamlining the corrosion inspection process.
Building on the field-validated design of its predecessor, the semi-automated HydroFORM™ scanner now integrates dual-axis encoders, delivering a complete 2-axis corrosion mapping solution without the need for an auxiliary scanner. This advancement facilitates the capture of high-resolution data of large surfaces in minimal time, providing more reliable data and deeper insights for repair and longevity assessment.
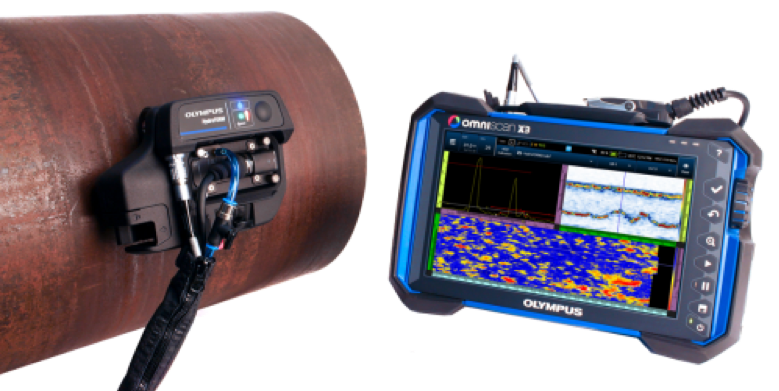
The HydroFORM™ scanner is a proven solution for inspecting internal corrosion in pipes. Its distinctive low-flow water-column design, coupled with foam gaskets, conforms seamlessly to surfaces, eliminating the need for a wedge. The reduced water requirement in the new probe streamlines efficiency, particularly during operations where continuous water feed might not be available. This accelerates the entire process, which can be particularly important when working in more dangerous or physically demanding environments.
The HydroFORM scanner's versatility extends to vertical and inverted scanning tasks, like monitoring tank walls for corrosion, thanks to its smooth-indexing magnetic wheels and enhanced bubble management. Moreover, the inclusion of gasket protectors significantly enhances the longevity of the foam gaskets, providing crucial protection when navigating rough profiles, welds, and surfaces reaching temperatures of 90°C (194°F).
Equipped with the ScanDeck™ module, the HydroFORM™ scanner is optimized for easy deployment and one-person operation, ensuring rapid and reliable PA scanning. When used with an OmniScan™ flaw detector, the ScanDeck™ module provides important feedback and remote functionalities, minimizing the need for direct operator interaction with the instrument.
Directly in the operator’s eyeline while scanning, status lights indicate which encoder is active, when the optimum index position has been reached, whether the coupling is sufficient, and if the maximum scan speed is exceeded. It also enables the HydroFORM™ operator to remotely start/stop and erase the data acquisition on the OmniScan™ unit. This information and remote-control capability not only reduce time-consuming tasks, but also improve the quality and reliability of the acquired PA data.
Highly adaptable, the HydroFORM scanner accommodates various inspection styles, serving as a manual scanner, a guided 2-axis encoding scanner, or compatible with semi-automated and automated auxiliary scanners for complex, large-area, and remote inspections.
When paired with the OmniScan X3 flaw detector, the HydroFORM scanner delivers exceptional near-surface resolution, accurately identifying the wall thickness in areas as small as 1 mm2 with precision. By combining a water column system with easy gate synchronization, the HydroFORM scanner and the OmniScan X3 detector make a complete PA solution for streamlined material inspection. This solution not only addresses present inspection needs but also anticipates and fulfills the evolving requirements of industries reliant on thorough corrosion mapping.
Learn more by visiting Evident.
Read the article online at: https://www.hydrocarbonengineering.com/special-reports/19022024/hydroform-scanner-the-complete-solution-for-comprehensive-corrosion-mapping/
You might also like
Get connected
Industrial operators that take advantage of the latest digital and automation asset performance management (APM) tools can look forward to improved operational efficiency, reduced downtime, and a proactive maintenance culture. Stacey Jones, ABB Energy Industries, explains.